Monitorowanie stabilności maszyny za pomocą danologii
Opublikowano 16 Lipca 2021 w Industry 4.0
Kontrola poprawności działania maszyny
Na czym polega skanowanie danych? Sygnały z czujników i (jeśli to możliwe) z siłowników są rejestrowane z wysoką częstotliwością, analizowane i łączone z procesem maszyny i programem sterowania. Dzięki temu operatorzy i/lub inżynierowie mogą uzyskać szczegółowy wgląd w maszynę i wykryć odchylenia oraz niespójności, takie jak niewspółosiowość czujników, nieprawidłowa konfiguracja, czy też zużycie części. Pozwala to ograniczyć występowanie mikroprzestojów i ułatwia znajdowanie głównej przyczyny przerywanej pracy maszyny oraz innych nieokreślonych problemów.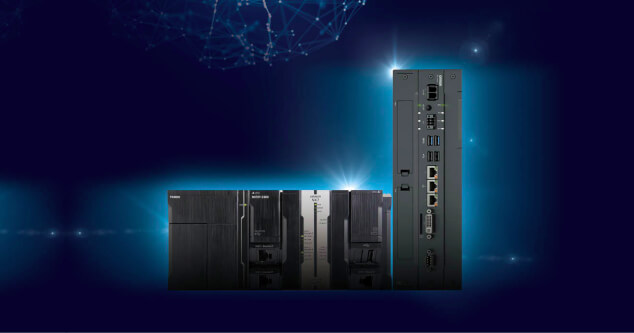
Monitorowanie maszyny
Dzięki stałemu monitorowaniu możliwe jest wykrywanie anomalii w procesach i jakości, odchyleń w trendach i przekazywanie efektywnych porad w zakresie konserwacji zapobiegawczej. Uzyskuje się także dostęp do czasu przełączania maszyny i większej ilości danych wejściowych dla szkoleń modelowych. Regularna aktualizacja modeli jest niezbędna do utrzymania i zwiększenia dokładności przewidywania.Zastosowanie sterownika SI Sysmac firmy OMRON
Czy wiesz, że OMRON oferuje sterownik maszyny z biblioteką Sysmac wykorzystującą sztuczną inteligencję? Możemy wesprzeć Twój zakład poprzez weryfikację koncepcji i pomóc we wdrożeniu sterownika SI do linii produkcyjnej. Firma OMRON oferuje również usługę „AI-as-a-service”, w ramach której dbamy się o pełne wdrożenie rozwiązania, aktualizacje, modernizacje i konserwację. Nawet systemy SI wymagają poświęcania im regularnej uwagi w celu poprawy i przystosowania do wykrytych zmian w działaniu maszyny i/lub procesu produkcyjnego.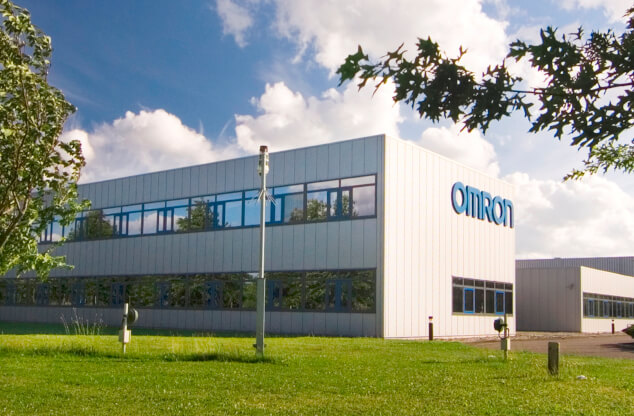
Studium przypadku: zakład OMRON Manufacturing of The Netherlands
Niedawno w zakładzie OMRON Manufacturing of The Netherlands (OMN) przeprowadzono projekt danologiczny w zakresie linii montażowej NX, skupiający się na maszynie do wstrzeliwania kołków w obudowy z tworzywa sztucznego.Maszyna wstrzeliwująca kołki jest wyposażona w kilka silników i czujników, które generują ponad 50 sygnałów jednocześnie. Celem tego projektu było monitorowanie wszystkich sygnałów naraz i wykrywanie nietypowych zdarzeń. Sterownik SI rejestrował sygnały co 2 milisekundy jako dane zdarzenia i gromadził je do analizy i wykrywania anomalii.
Jeden z najczęściej występujących problemów w tej maszynie był spowodowany zaginaniem i podawaniem materiału przez silniki, gdy maszyna nie może od razu w prawidłowy sposób poruszać rolkami. Problem ten wymaga podjęcia działań konserwacyjnych, które powodują zatrzymanie całej linii produkcyjnej na prawie godzinę. Dzięki funkcji wykrywania anomalii usterki można zidentyfikować wcześniej, a do inżynierów i pracowników serwisu przesyłany jest komunikat alarmowy. W przypadku maszyny wstrzeliwującej kołki alarm jest wszczynany na kilka godzin przed wystąpieniem poważnego problemu. Tak wczesne powiadomienie alarmowe pozwala zapobiec przestojowi maszyny, umożliwiając podjęcie szybkich działań konserwacyjnych, a ponadto zapewnia sugestię prostej korekty, która nie spowoduje znacznego przestoju.
Co więcej, drobne zmiany w działaniu maszyny są niewykrywalne dla ludzi. Jeśli maszyna zwalnia swoją pracę przy każdym cyklu produkcyjnym o kilka milisekund tygodniowo, zarówno operatorzy, jak i inżynierowie nie będą w stanie zauważyć tych zmian. Jednak z biegiem czasu praca maszyny może stać się o 10% wolniejsza, a jej dzienny potencjał produkcyjny o 15% niższy. Główną przyczynę tego problemu wykryto poprzez monitorowanie zachowania wszystkich sygnałów za pomocą modeli wykrywania anomalii. Dzięki temu można było dokonać regulacji, aby utrzymać wysoką wydajność maszyny.
Czy chcesz wykorzystać pełną wartość, jaką niosą za sobą Twoje dane przemysłowe lub zmagasz się z problemem, którego rozwiązanie jest Twoim zdaniem ukryte w zgromadzonych danych? Pobierz poniższy oficjalny raport, aby dowiedzieć się więcej.